Advantages
Efficiency in Handling and Transport:
- Time-Saving: Cable reel flat cars significantly reduce the time required to load, transport, and deploy cable reels. The mechanized handling minimizes manual labor, speeding up operations.
- Automated Deployment: Many models are equipped with motorized systems to rotate the reels, allowing for automated and precise deployment of cables.
High Load-Bearing Capacity:
- Heavy-Duty Design: These flat cars are built to carry heavy and bulky reels, which can hold large quantities of cable. This capacity is crucial for industrial applications where significant amounts of cable need to be transported and laid out.
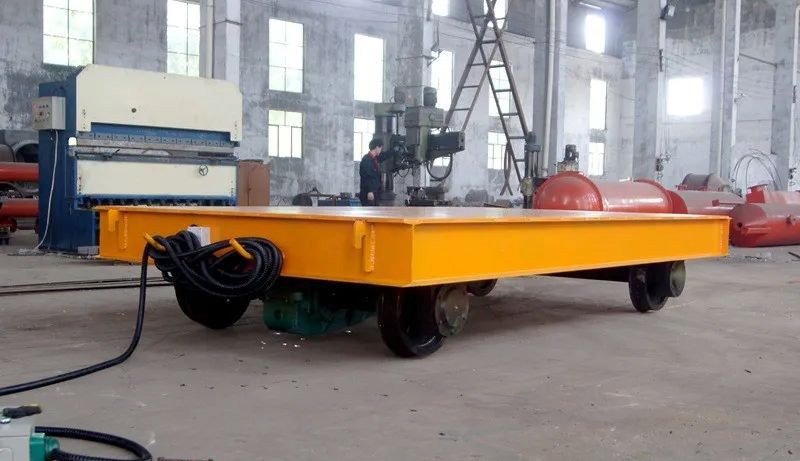
Improved Safety:
- Secure Transport: The design includes features like support structures, chocks, and adjustable mounts to secure the reels during transit. This prevents the reels from shifting or rolling, reducing the risk of accidents.
- Reduced Manual Handling: Automated features reduce the need for manual lifting and handling of heavy reels, minimizing the risk of worker injuries.
Versatility and Adaptability:
- Various Reel Sizes: Cable reel flat cars can accommodate different sizes and types of reels, making them versatile for various applications across industries like construction, utilities, and telecommunications.
- Terrain Adaptability: Some models are designed to operate on various terrains, both indoor and outdoor, enhancing their utility in diverse environments.
Enhanced Productivity:
- Continuous Operation: In environments like manufacturing and logistics, these flat cars ensure continuous operation, reducing downtime and increasing overall productivity.
- Flexibility: The ability to move along rails or self-propel across different areas allows for flexible use in complex industrial layouts.
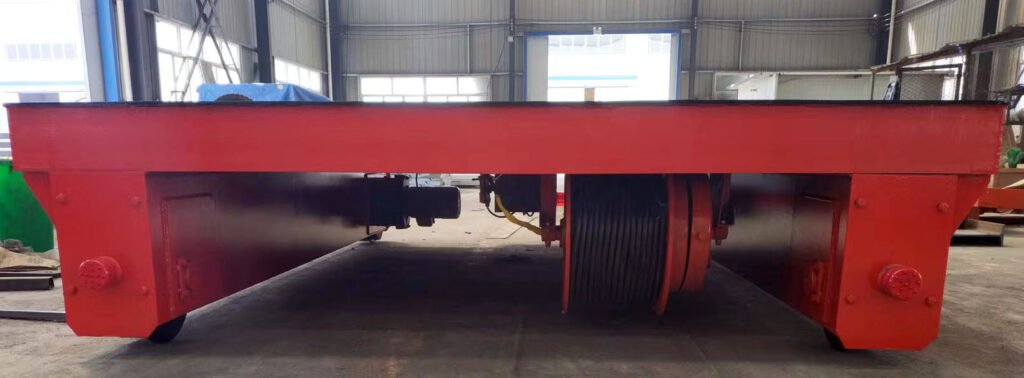
Disadvantages
High Initial Cost:
- Investment: The purchase and installation of cable reel flat cars represent a significant initial investment. This includes the cost of the flat cars themselves and any associated infrastructure like tracks or power systems.
Maintenance Requirements:
- Regular Maintenance: These machines require regular maintenance to ensure optimal performance and longevity. This includes mechanical inspections, lubrication, and potential repairs, which can incur additional costs and downtime.
- Specialized Parts: The need for specialized parts and trained personnel to maintain and repair these systems can further increase operational costs.
Operational Limitations:
- Track Dependency: For rail-based models, the flat car’s movement is restricted to the layout of the tracks. This can limit flexibility in operations and require additional planning for track placement and maintenance.
- Complex Terrain: While some models are adaptable to various terrains, extremely rough or uneven surfaces can still pose challenges, potentially limiting their use in certain environments.
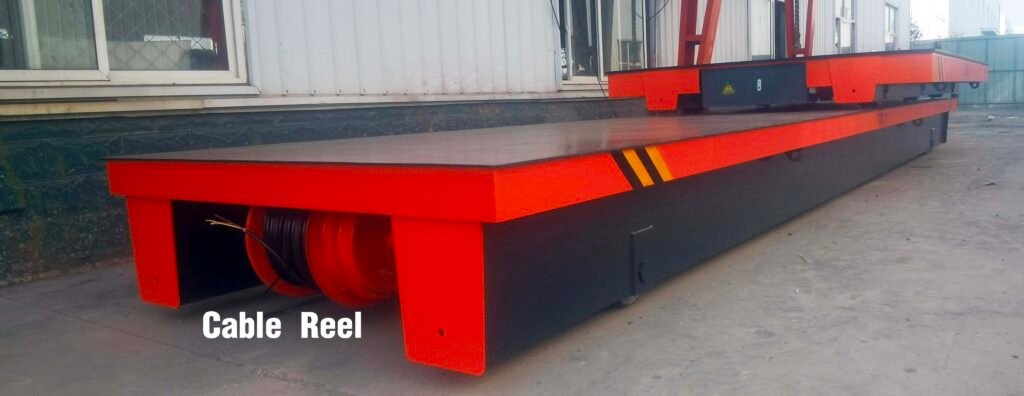
Space Requirements:
- Storage and Operation: These vehicles require adequate space for both storage and operation. In facilities with limited space, this can be a constraint, necessitating careful planning and layout design.
Power Supply Dependency:
- Electricity or Hydraulics: Cable reel flat cars often rely on an external power supply, such as electricity or hydraulics, to function. This dependency can be a disadvantage in areas with unstable power supplies or where extensive cabling is impractical.
Complexity of Integration:
- System Integration: Integrating cable reel flat cars into existing material handling systems can be complex, requiring significant planning and potential modifications to current workflows. This integration process can be time-consuming and costly.
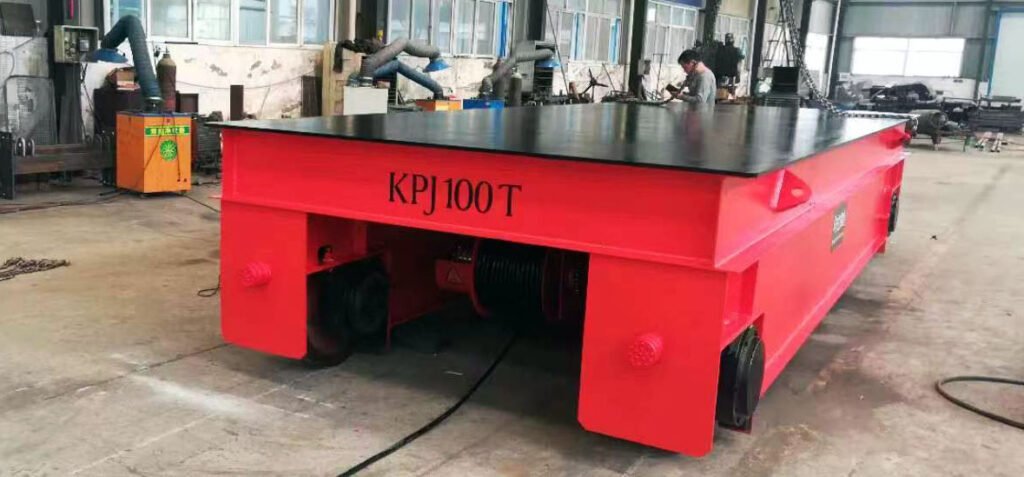
Conclusion
Cable reel flat cars offer significant advantages in terms of efficiency, safety, and versatility for industrial material handling, particularly in transporting and deploying large and heavy cable reels. However, they also come with challenges, including high initial costs, maintenance requirements, and certain operational limitations. When considering the adoption of cable reel flat cars, it’s essential to weigh these advantages and disadvantages in the context of specific operational needs and constraints. By doing so, industries can make informed decisions that enhance productivity and safety while managing costs and logistical complexities.