In the dynamic field of industrial automation and logistics, the versatility and efficiency of material handling equipment are paramount. Electric flat cars, known for their robust functionality and adaptability, are essential in various industrial settings. A critical aspect of their design is their ability to navigate curved tracks efficiently. This article delves into how electric flat cars adapt to curved tracks, focusing on the technological innovations that enable this capability.
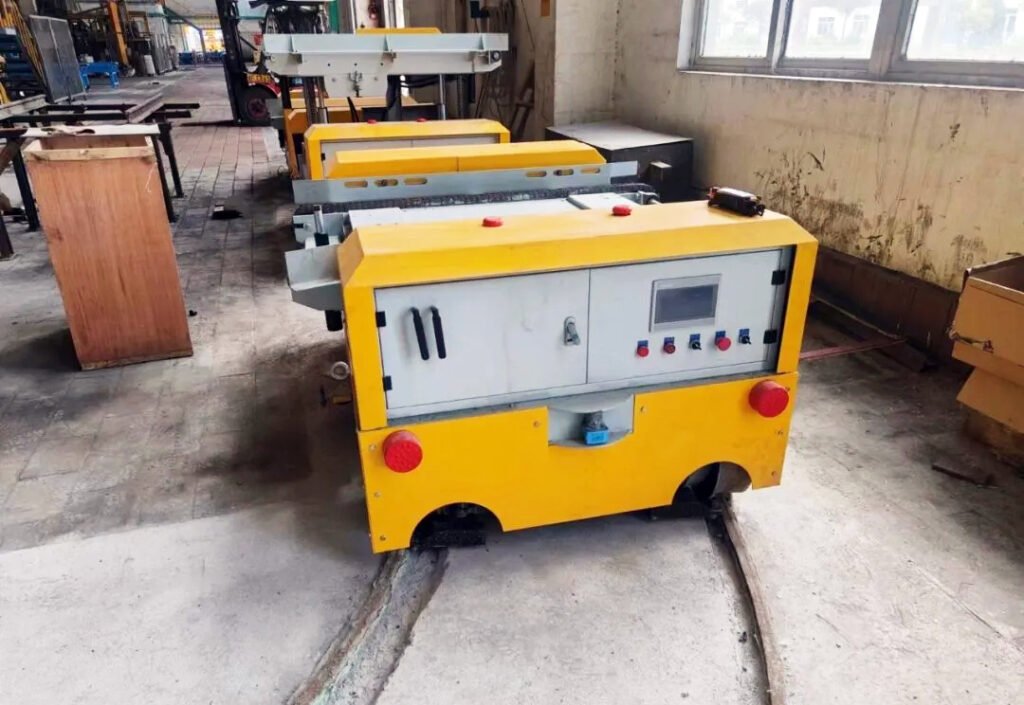
The Importance of Curved Track Navigation
In many industrial environments, space constraints and complex layouts necessitate the use of curved tracks. Electric flat cars must navigate these curves smoothly to maintain efficiency and safety. The ability to handle curved tracks without compromising on speed, stability, or safety is a testament to the advanced engineering behind these vehicles.
Role of the Motor Controller
The motor controller is the core component that plays a vital role when an electric flat car runs on curved rails. Upon receiving the turning signal, the controller initiates a series of precise calculations and adjustments to control the motor speed and steering accurately. This ensures that the flat car can pass the curve smoothly.
- Signal Processing and Adjustment
Immediate Response Once a turning signal is detected, the motor controller begins to process this information instantaneously. Advanced algorithms come into play, determining the optimal speed and steering angle required to navigate the curve.
Real-time Calculations These calculations are done in real-time, allowing for dynamic adjustments as the flat car approaches and traverses the curve. This capability reflects the intelligent and adaptive nature of modern electric flat cars.
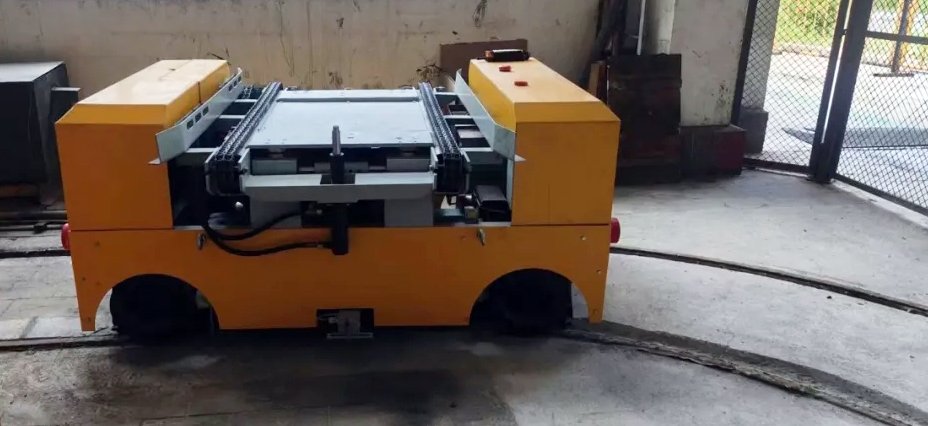
Inner and Outer Track Dynamics
The design of the tracks themselves is crucial for the successful navigation of curves. The interaction between the inner and outer tracks provides the necessary conditions for stability and control.
- Inner Track Friction
Stability Maintenance The inner track provides the essential friction needed for the electric flat car to maintain a stable speed during travel. This friction is vital for preventing slippage and ensuring a consistent motion through the curve. - Outer Track Limitation
Trajectory Control The outer track limits the driving trajectory of the flat car, preventing it from deviating. This design ensures that the vehicle remains on the intended path, enhancing both safety and operational reliability.
Drum-Shaped Wheel Design
A unique feature of electric flat cars that significantly aids in navigating curved tracks is the drum-shaped wheel design. This design addresses the lateral forces generated by centrifugal force during a turn.
- Lateral Force Management
Automatic Adjustment The drum-shaped wheels can automatically adjust their direction to counteract the lateral forces encountered during a turn. This adjustment is crucial for maintaining stability and preventing derailment.
Enhanced Stability By effectively managing these forces, the drum-shaped wheels enhance the overall stability of the electric flat car, ensuring smooth and safe navigation through curves.
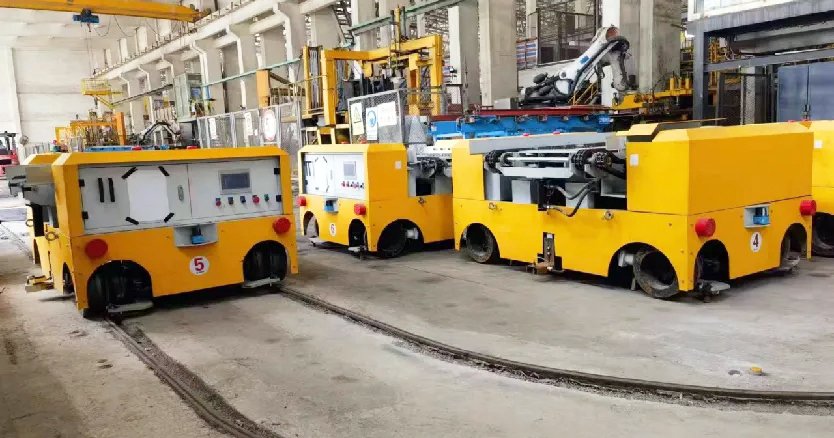
Advanced Algorithm Technology in Motor Controllers
The integration of advanced algorithm technology within the motor controllers further enhances the ability of electric flat cars to navigate complex road conditions, including curves.
- Real-Time Monitoring and Adjustment
Operating Status Monitoring The motor and controller continuously monitor the operating status of the flat car in real-time. This monitoring includes tracking various parameters such as speed, position, and trajectory.
Dynamic Parameter Adjustment Based on the real-time data, the motor controller adjusts the driving parameters dynamically. This adjustment process ensures that the flat car maintains a stable driving status under varying road conditions, including curves. - Efficiency and Safety Improvements
Optimized Performance The intelligent control methods employed by the motor controllers not only improve the operational efficiency of the electric flat car but also significantly enhance its safety and reliability.
Preventive Measures By anticipating and responding to changes in real-time, these systems can prevent potential issues before they escalate, thereby ensuring a smoother and safer operation.
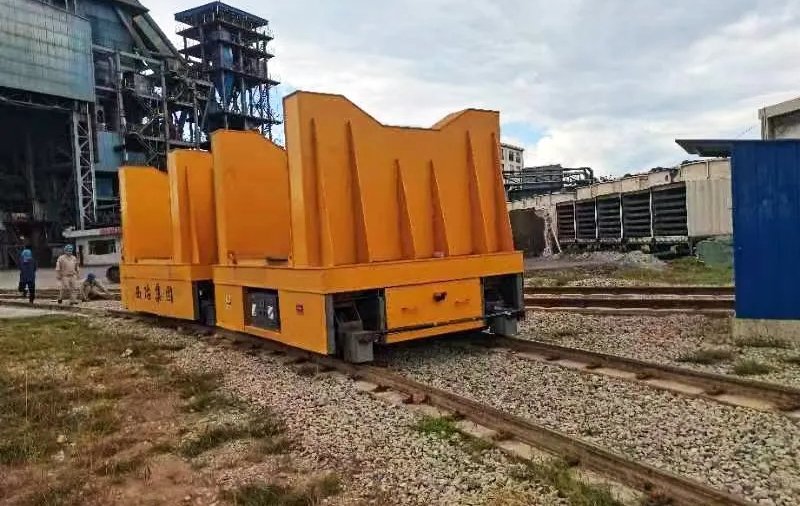
Conclusion
Navigating curved tracks is a complex challenge that electric flat cars have adeptly overcome through innovative design and advanced technology. The precise control facilitated by motor controllers, the synergistic function of inner and outer tracks, and the adaptive capabilities of drum-shaped wheels all contribute to the seamless operation of these vehicles in industrial settings. The integration of advanced algorithm technology further ensures that electric flat cars operate efficiently and safely under various conditions, making them indispensable in modern material handling and logistics.
By harnessing these technological advancements, industries can achieve greater efficiency, reduce operational risks, and enhance overall productivity. As electric flat cars continue to evolve, their ability to adapt to complex track configurations will only improve, further solidifying their role as critical assets in industrial automation.