In the realm of modern logistics and production, the adoption of intelligent robotics has significantly transformed operations. One notable advancement is the use of Rail Guided Vehicles (RGVs), which are wheeled robots designed to enhance efficiency through automation. By integrating RFID (Radio-Frequency Identification) and barcode technology, RGVs can achieve automated material identification and access, thereby optimizing production processes and reducing labor costs.
The Functionality of RGVs in Logistics
RGVs are versatile pieces of equipment capable of autonomous programming and task execution. They communicate seamlessly with host computers or Warehouse Management Systems (WMS), ensuring a streamlined flow of operations. The integration of RFID and barcode technologies allows RGVs to automatically identify and manage materials, enhancing production efficiency and operational accuracy.
RGVs can be categorized based on their movement modes into two main types: linear path RGVs and circular orbit RGVs. Each type serves distinct purposes and offers unique advantages in various industrial applications.
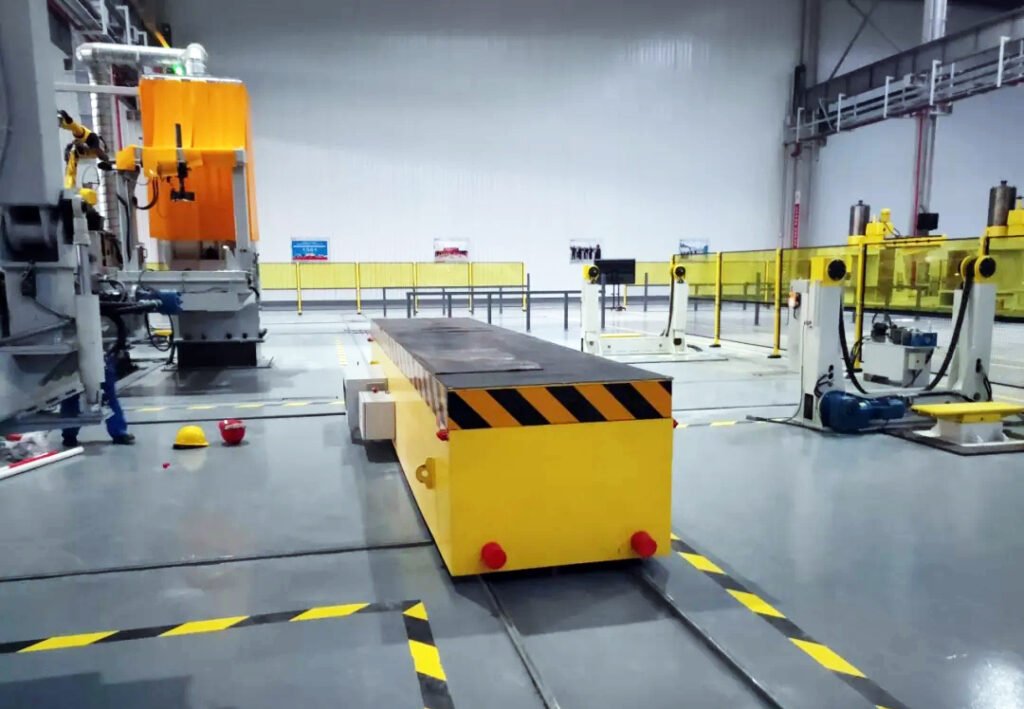
Linear Path RGVs
Linear path RGVs are primarily tasked with transporting materials along a straight path from one location to another. This straightforward design is instrumental in achieving seamless connections between different points in the production line. The precision and speed of linear path RGVs make them ideal for environments where quick and accurate material transport is crucial. Their efficiency in moving materials reduces bottlenecks and enhances the overall throughput of production lines.
Circular Orbit RGVs
Circular orbit RGVs, on the other hand, are designed for more complex operational environments. Their circular track design allows these RGVs to switch directions and tasks swiftly, minimizing scheduling and waiting times. This agility significantly improves the efficiency of system operations. One of the key advantages of circular orbit RGV systems is their ability to operate multiple RGVs simultaneously. This multi-robot coordination maximizes the use of production line space and prevents congestion, which is common when a single robot handles multiple tasks.
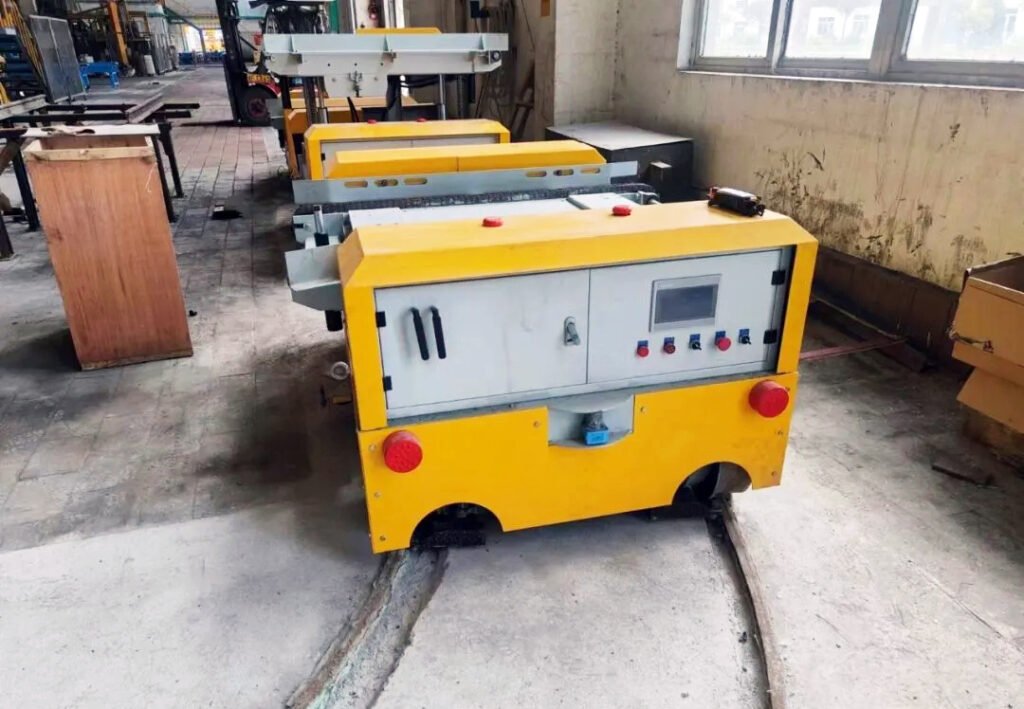
Moreover, the scalability of circular orbit RGV systems offers flexibility in adjusting the number of robots based on production needs. This adaptability makes it possible to scale operations up or down to meet varying demands, ensuring optimal resource utilization and production efficiency.
Integration of RFID and Barcode Technologies
The use of RFID and barcode technologies in RGV systems plays a pivotal role in automating material handling processes. RFID technology involves the use of electromagnetic fields to automatically identify and track tags attached to objects. Barcodes, consisting of visual patterns that can be scanned and interpreted by machines, serve a similar purpose. When integrated into RGV systems, these technologies enable the automatic identification of materials, which is essential for accurate and efficient logistics operations.
RFID tags and barcodes can be attached to materials or containers, allowing RGVs to read and process the information without human intervention. This automated identification process reduces errors associated with manual data entry and enhances the speed of operations. Additionally, it ensures that materials are accurately tracked throughout the production process, providing real-time data that is crucial for effective inventory management and production planning.
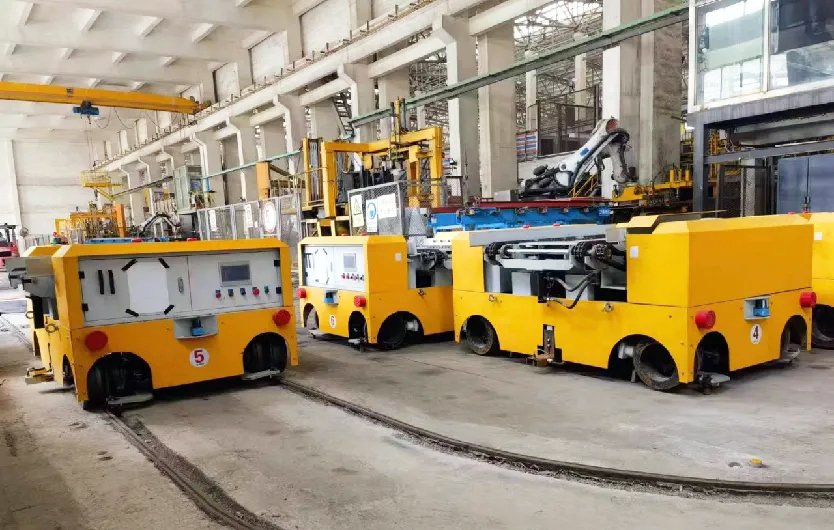
Advantages of Automated Material Handling with RGVs
- Increased Efficiency Automated identification and handling of materials significantly reduce the time required for manual processes, leading to faster production cycles and higher throughput.
- Cost Reduction By minimizing the need for manual labor, RGV systems lower operational costs. This reduction in labor costs, combined with increased efficiency, results in significant savings for businesses.
- Enhanced Accuracy The integration of RFID and barcode technologies ensures precise tracking and handling of materials, reducing the likelihood of errors that can occur with manual processes.
- Scalability and Flexibility RGV systems, particularly circular orbit RGVs, offer the flexibility to adjust the number of robots in operation, allowing businesses to scale their operations according to demand.
- Space Optimization The ability to operate multiple RGVs simultaneously and efficiently manage production line space helps avoid congestion and optimize the use of available resources.
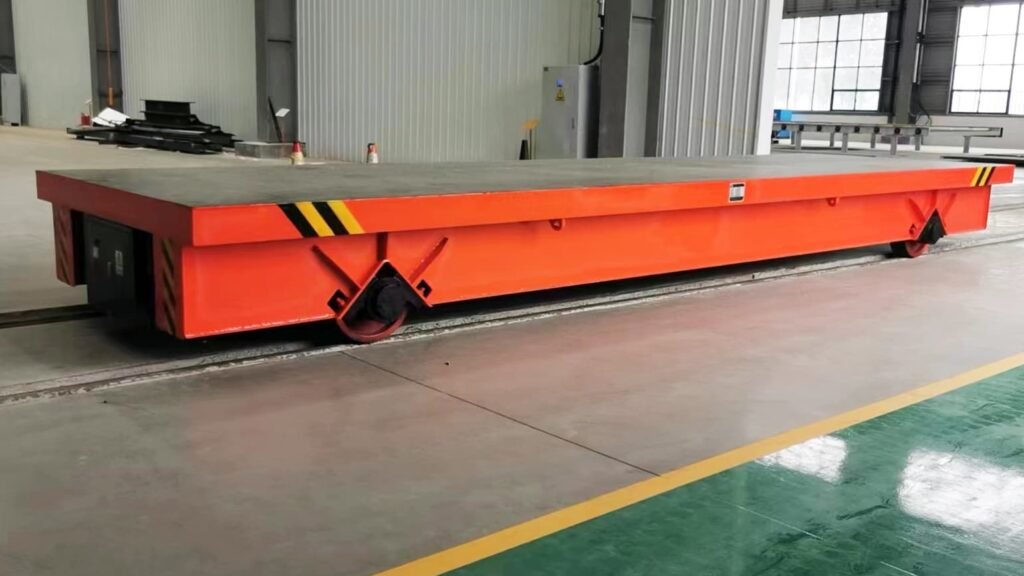
Conclusion
The implementation of RGVs integrated with RFID and barcode technologies represents a significant leap forward in modern logistics and production. The distinct advantages offered by linear path and circular orbit RGVs make them indispensable in various industrial applications. While linear path RGVs provide precise and efficient material transport, circular orbit RGVs offer high flexibility and scalability, making them ideal for complex production environments.
Incorporating these advanced robotic systems into logistics operations not only enhances efficiency and accuracy but also reduces costs and improves overall productivity. As industries continue to evolve, the role of RGVs in automated material handling is set to become even more prominent, driving further advancements in logistics and production technologies.