An Automated Guided Vehicle (AGV) is a self-operating, unmanned vehicle designed to transport materials within industrial settings such as factories, warehouses, and distribution centers. These vehicles follow a series of predetermined instructions, cues, or signals to navigate and perform tasks autonomously, without the need for a human operator. AGVs are integral to modern material handling systems, offering enhanced efficiency, safety, and reliability in various industrial applications.
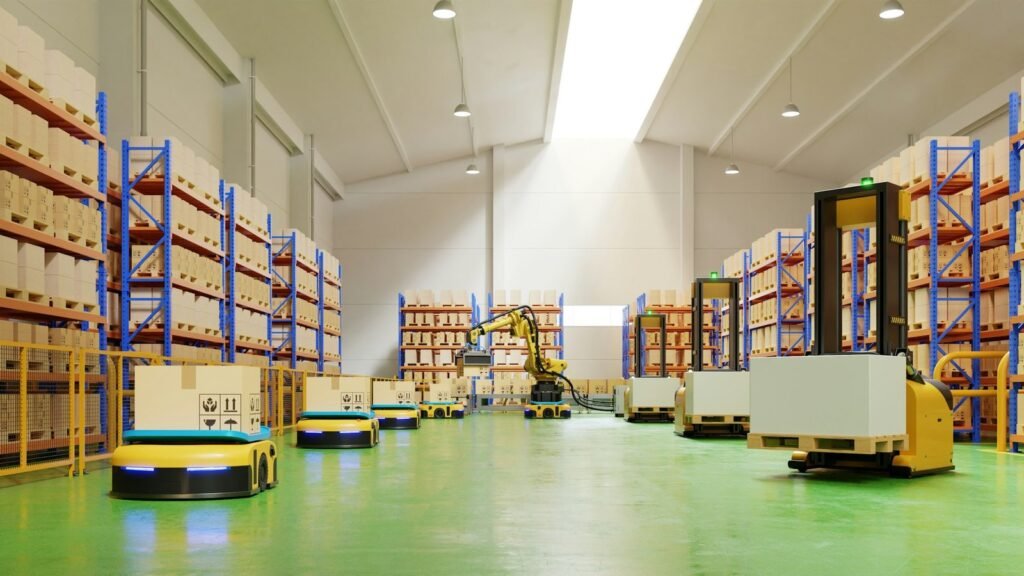
Key Features and Types of AGVs
AGVs come in various types, each tailored to specific tasks and environments. Here are some of the most common types:
- Forked AGVs:
- These AGVs are equipped with forks similar to those on forklifts and are designed to lift and transport materials, most often pallets. Unlike automated forklifts, forked AGVs are built exclusively for automated operation and cannot be manually driven[1].
2. Loading Type AGVs:
- These AGVs have the capability to load goods on top, making them versatile for transporting items of various shapes and sizes. They are commonly used in factories, warehouses, and even research facilities and hospitals due to their flexibility and large loading space[2].
3. Low-Floor AGVs:
- Characterized by their very low height, these AGVs are ideal for transporting machinery parts, electronic equipment, and medicines. Their low profile allows them to navigate under equipment and through tight spaces[2].
4. Towing AGVs:
- Also known as tuggers, these AGVs are designed to pull carts, trailers, or other wheeled devices. They are particularly useful in environments with ample aisle space and are capable of moving large volumes of goods efficiently[2].
5. Flat Body/Heavyweight AGVs:
- These AGVs are designed for transporting heavy loads, often exceeding 800 kg. Their flat body design ensures stability during transport and can accommodate a wide range of industrial needs, such as moving steel materials, car frames, and large machinery parts[2].
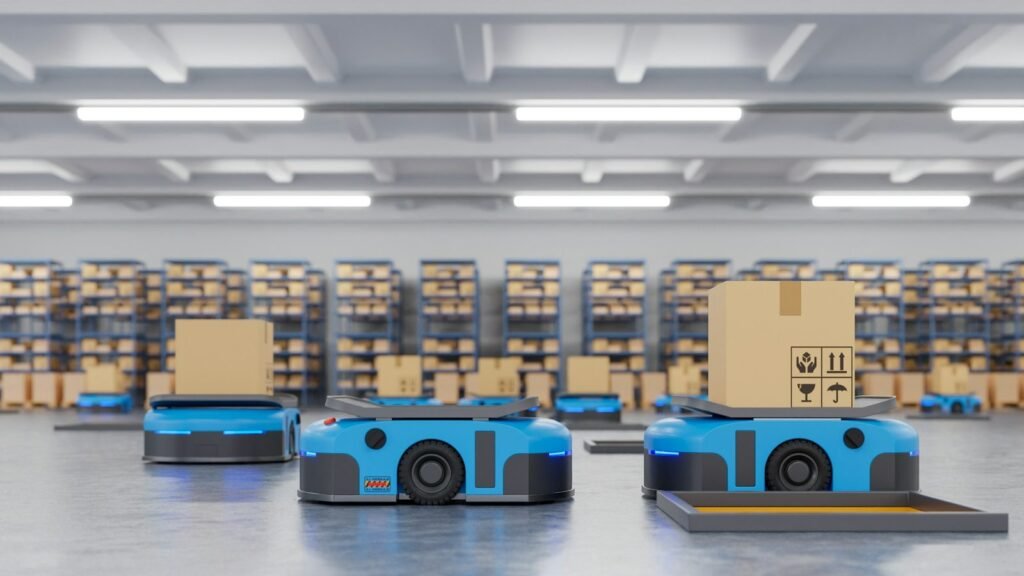
How AGVs Work
AGVs operate based on various guidance systems, which can include:
- Magnetic Tape or RFID Tags:
- These systems use physical guidelines embedded in the floor to navigate a precise path. This method is highly reliable for continuous transport operations due to the low risk of signal loss and errors[2].
- Laser Guidance:
- Laser-guided AGVs use reflective markers placed around the facility to determine their position and navigate. This system allows for more flexible routing and can adapt to changes in the environment[3].
- Vision Guidance:
- Vision-guided AGVs use cameras and image processing to navigate and avoid obstacles. This advanced technology enables real-time adjustments and is suitable for dynamic environments[3].
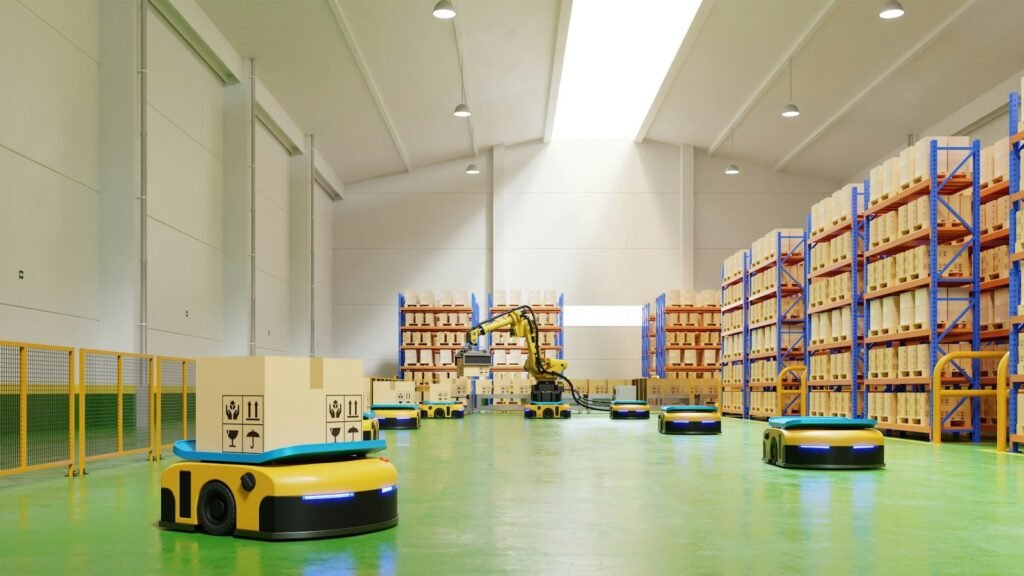
Benefits of AGVs
- 24-Hour Operation:
- AGVs can operate continuously without breaks, significantly increasing productivity and reducing the need for human labor[2].
- Improved Safety:
- By automating material handling tasks, AGVs reduce the risk of workplace accidents and injuries. They are equipped with safety features such as obstacle detection sensors and emergency stop buttons to ensure safe operation[2][3].
- Enhanced Efficiency:
- AGVs streamline material handling processes, reducing delays and ensuring a consistent flow of materials. This efficiency translates to higher productivity and lower operational costs[3].
- Flexibility and Scalability:
- AGVs can be easily integrated into existing workflows and scaled up as needed. Their modular design allows for customization to meet specific industrial requirements[2].
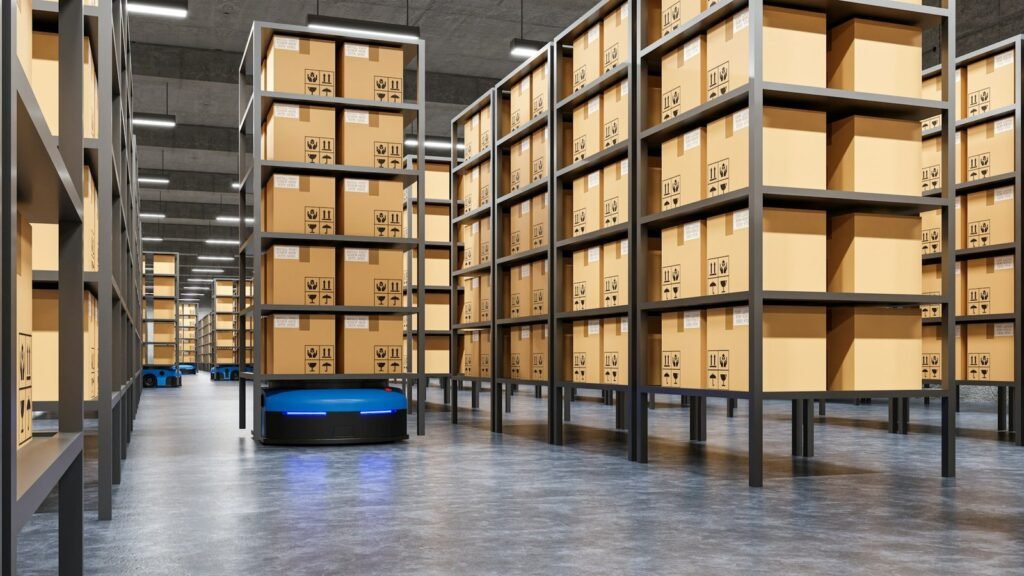
Applications of AGVs
AGVs are used in a variety of settings, including:
- Manufacturing:
- In manufacturing environments, AGVs transport raw materials, components, and finished goods between workstations and storage areas, optimizing the production process and reducing the likelihood of stoppages[3].
- Warehousing and Distribution:
- AGVs are employed to move pallets, containers, and racks within warehouses and distribution centers. They facilitate efficient loading, unloading, and storage operations, ensuring timely delivery of goods[3].
- Hospitals:
- In healthcare settings, AGVs are used to transport pharmaceuticals, medical supplies, and meals, improving operational efficiency and reducing the risk of contamination[2].
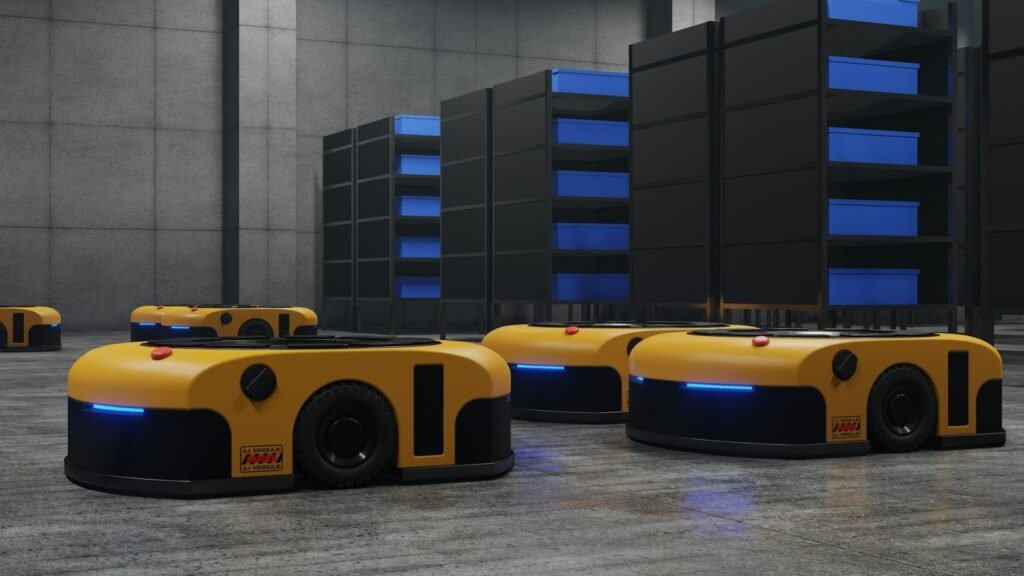
Conclusion
Automated Guided Vehicles (AGVs) represent a significant advancement in material handling technology. By automating the transportation of goods within industrial environments, AGVs enhance efficiency, safety, and reliability. Their diverse types and advanced guidance systems make them suitable for a wide range of applications, from manufacturing and warehousing to healthcare. As industries continue to seek ways to optimize operations and reduce costs, the adoption of AGVs is likely to grow, driving further innovation and improvement in material handling processes.
By understanding the capabilities and benefits of AGVs, businesses can make informed decisions about integrating these advanced vehicles into their operations, ultimately achieving greater productivity and operational excellence.