The trackless flat car, also known as a trackless transfer cart or AGV (Automated Guided Vehicle), operates without the need for fixed rails, providing flexible and efficient material handling solutions. Here’s an introduction to its working principle

Power Source
Trackless flat cars are typically powered by batteries, often rechargeable lithium-ion or lead-acid batteries. These batteries provide the necessary power to drive the motors and operate the control systems.
Drive System
The cart is equipped with a drive system, which includes motors connected to wheels. These motors can be electric or hydraulic, depending on the design. The drive system enables the cart to move forward, backward, and make turns.
Steering Mechanism
Trackless flat cars use a steering mechanism that allows for directional control. This can be a differential steering system (like in tank steering) where the wheels on either side of the cart operate at different speeds, or it can use a more traditional steering system with steerable wheels.
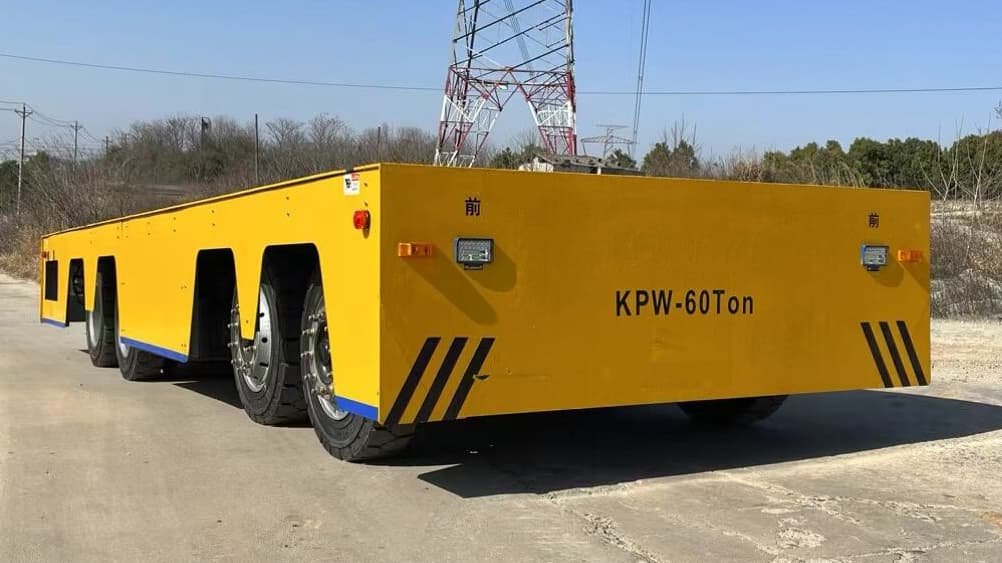
Control System
The control system manages the movement and operations of the cart. This can include:
Manual Control: Operated by a human using a remote control or onboard controls.
Automated Control: Using programmed paths and autonomous navigation technologies like lasers, magnetic strips, or GPS.
Navigation and Guidance
For automated trackless flat cars, navigation and guidance are critical. Common methods include:
Laser Guidance: Uses lasers and reflectors placed in the operating environment to determine the cart’s position and navigate.
Magnetic Strips: Embedded in the floor, the cart follows these strips using onboard sensors.
Optical Guidance: Uses cameras and visual markers to navigate.
GPS/RTLS (Real-Time Locating Systems): For outdoor or large indoor facilities, GPS or RTLS can provide precise location data.
Safety Systems
Trackless flat cars are equipped with various safety features to prevent accidents and ensure smooth operation. These include:
Obstacle Detection: Using sensors like LiDAR, ultrasonic sensors, or infrared sensors to detect and avoid obstacles.
Emergency Stop: Buttons or remote controls that allow operators to halt the cart immediately in case of an emergency.
Speed Control: Automatic adjustment of speed based on load, path, and proximity to obstacles.
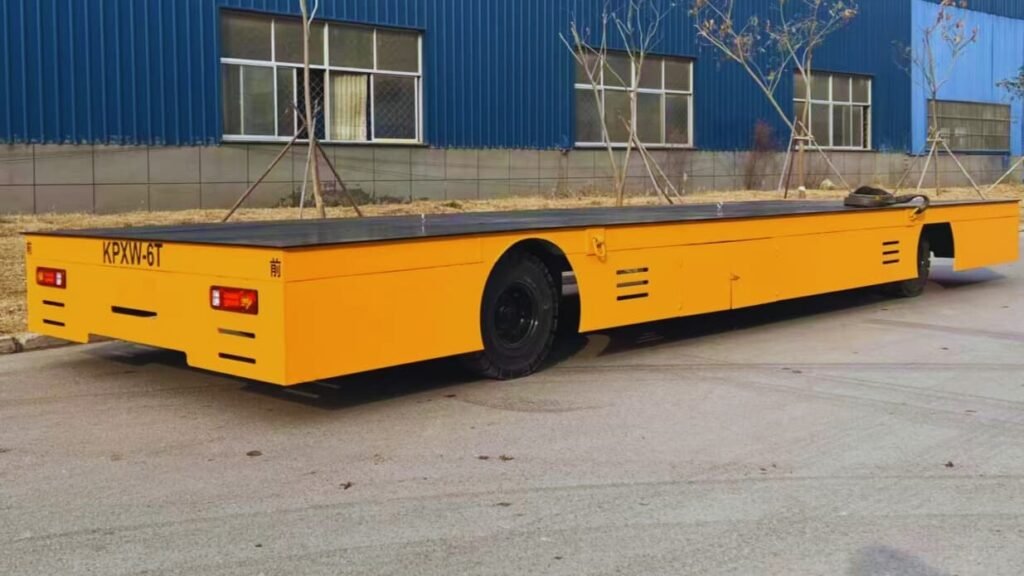
Advantages
- Flexibility: Can navigate various paths without being confined to fixed rails.
- Versatility: Suitable for different environments and applications.
- Scalability: Easy to expand and reconfigure without the need for additional infrastructure.
- Efficiency: Enhances material handling efficiency by automating transport tasks.
Applications
- Manufacturing: Moving parts and assemblies between workstations.
- Warehousing: Handling goods within a storage facility.
- Automotive Industry: Transporting vehicle components.
- Hospitals: Delivering supplies and equipment.
- Construction: Moving materials around construction sites.
Maintenance and Operation Tips
- Regular Charging: Ensure batteries are charged properly and maintain good battery health.
- Routine Inspections: Regularly check the cart for wear and tear, especially the drive and steering systems.
- Software Updates: Keep navigation and control software updated for optimal performance.
- Operator Training: Ensure operators are trained to use both manual and automated controls safely.
By understanding the working principle and advantages of trackless flat cars, you can effectively integrate them into your operations to improve efficiency and flexibility in material handling tasks.